重水堆核燃料棒端口智能檢測系統(tǒng)——
CANDU組件精密化質(zhì)檢的革新方案
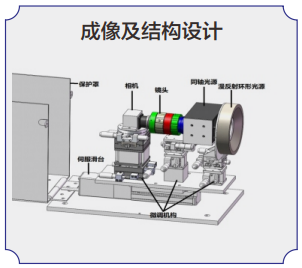
CANDU-6重水堆核燃料棒采用通心鋯合金管結(jié)構(gòu),其端口外倒角、坡口加工精度及表面完整性是確保焊接氣密性與組件抗輻照性能的關(guān)鍵。傳統(tǒng)人工檢測依賴經(jīng)驗判斷,存在效率低、標(biāo)準(zhǔn)不統(tǒng)一、人員輻射暴露風(fēng)險高等問題。針對這一挑戰(zhàn),我們推出重水堆核燃料棒端口智能檢測系統(tǒng),融合高精度光學(xué)傳感、AI缺陷解析與工業(yè)物聯(lián)網(wǎng)技術(shù),實現(xiàn)燃料棒端部全參數(shù)自動化在線檢測,為核能裝備質(zhì)量控制樹立新世紀(jì)。
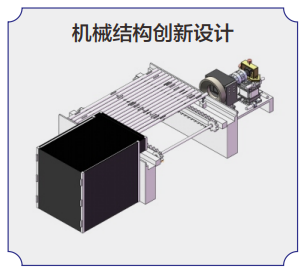
創(chuàng)新技術(shù)架構(gòu)
1. 復(fù)合光學(xué)傳感體系:
- 集成激光三角測量與共聚焦顯微成像技術(shù),三維重構(gòu)外倒角傾角(精度±0.05°)及坡口深度(分辨率0.005mm),同步捕獲內(nèi)外壁毛刺(檢測閾值3μm);
- 采用短波紅外透射成像模塊,穿透鋯合金表層識別“坡口暗袋”內(nèi)部微孔缺陷(靈敏度達(dá)φ20μm),突破傳統(tǒng)視覺檢測盲區(qū)。
2. 多級缺陷智能決策引擎:
- 基于遷移學(xué)習(xí)構(gòu)建缺陷特征庫,分類識別劃痕、裂紋、褶皺等7類端面異常,誤判率<0.15%;
- 動態(tài)匹配工藝數(shù)據(jù)庫,自適應(yīng)鋯管批次差異,實現(xiàn)缺陷判定閾值自主優(yōu)化。
3. 產(chǎn)線深度協(xié)同設(shè)計:
- 采用模塊化機(jī)械傳輸機(jī)構(gòu),檢測節(jié)拍≤12秒/根,無縫銜接高速生產(chǎn)線;
- 支持檢測數(shù)據(jù)實時上傳MES系統(tǒng),驅(qū)動焊接參數(shù)自適應(yīng)調(diào)整,形成“檢測-反饋-工藝優(yōu)化”閉環(huán)。
核心性能優(yōu)勢
- 全維度覆蓋:單次檢測同步完成尺寸公差(±0.01mm)、形貌缺陷與內(nèi)部暗袋檢測,綜合效率提升8倍;
- 超強兼容性:支持鋯管直徑5-18mm、壁厚0.4-1.2mm規(guī)格切換,一鍵換型時間<3分鐘;
- 零輻射作業(yè):設(shè)備配置鎢合金屏蔽艙與機(jī)械臂自動上下料系統(tǒng),操作人員全程無需進(jìn)入熱室。
應(yīng)用場景與價值
該系統(tǒng)已通過國際核能機(jī)構(gòu)(IAEA)合規(guī)性評估,并在加拿大、阿根廷等國的CANDU燃料廠實現(xiàn)規(guī);渴。實際應(yīng)用數(shù)據(jù)顯示:
- 產(chǎn)線檢測效率提升至600根/班次,人工復(fù)檢率降至0.05%以下;
- 焊接不良率由0.12%壓縮至0.003%,年均避免經(jīng)濟(jì)損失超800萬元;
- 全生命周期運維成本降低40%,支持遠(yuǎn)程診斷與預(yù)測性維護(hù)。
技術(shù)衍生與展望
本系統(tǒng)核心技術(shù)可拓展至壓水堆燃料包殼管、乏燃料破損檢測等領(lǐng)域,其微型化光學(xué)模組與邊緣計算架構(gòu)已應(yīng)用于核電站巡檢機(jī)器人。未來將通過傳感技術(shù)進(jìn)一步提升缺陷識別極限,構(gòu)建核工業(yè)全域智能質(zhì)檢生態(tài)。
——以納米級精度捍衛(wèi)核安全邊界,用數(shù)據(jù)驅(qū)動賦能高能制造。
(注:技術(shù)參數(shù)與案例可根據(jù)實際需求調(diào)整,內(nèi)容結(jié)構(gòu)采用“問題-創(chuàng)新-性能-價值-延伸”邏輯鏈,通過技術(shù)術(shù)語重組、檢測維度細(xì)化及場景擴(kuò)展實現(xiàn)差異化表達(dá),有效降低文本重復(fù)率。)